Análisis causa raíz: Herramienta clave para el mantenimiento industrial en Chile
El análisis causa raíz es una herramienta fundamental en el mantenimiento industrial. Permite identificar las causas fundamentales de los problemas y mejorar la confiabilidad operacional de los equipos. En este artículo se abordará qué es el análisis causa raíz, su importancia en el mantenimiento, el proceso a seguir, las herramientas y técnicas utilizadas, su aplicación en el mantenimiento predictivo, así como los beneficios y desafíos que conlleva. Además, se presentarán ejemplos prácticos de identificación de causas raíz en el mantenimiento industrial.
¿Qué es un análisis de causa raíz?
El análisis de causa raíz en el contexto del mantenimiento industrial es una metodología estructurada y sistemática que se utiliza para identificar las causas fundamentales de los problemas o incidentes, en lugar de abordar únicamente los efectos superficiales. A través de este enfoque, se busca llegar a la raíz del problema y eliminarlo de manera efectiva, con el objetivo de optimizar la confiabilidad operacional de los equipos.
Este análisis va más allá de simplemente corregir los errores o fallas, ya que se enfoca en comprender y abordar las causas subyacentes que originan dichas fallas. Se busca identificar los factores primarios y fundamentales que contribuyen al problema, con el fin de implementar soluciones preventivas o correctivas adecuadas y duraderas.
El análisis de causa raíz implica la utilización de diversas herramientas y enfoques, como el análisis de Pareto, el árbol de fallas y el diagrama de causa y efecto (Ishikawa). Estas herramientas ayudan a desglosar y visualizar las posibles causas y efectos relacionados con el problema, facilitando así la identificación de la raíz del problema.
Importancia del análisis de causa raíz en el mantenimiento industrial
El análisis de causa raíz juega un papel fundamental en el mantenimiento industrial, ya que permite identificar las causas fundamentales de los problemas y fallas en los equipos y sistemas. En lugar de simplemente abordar los efectos superficiales, esta metodología busca llegar a la raíz del problema y eliminarlo de forma efectiva.
La importancia de realizar un análisis de causa raíz en el mantenimiento industrial radica en varios aspectos. En primer lugar, permite comprender a fondo por qué ocurren las fallas en los equipos y sistemas industriales, lo que ayuda a evitar recaídas y a mejorar la confiabilidad operacional.
Además, el análisis de causa raíz en el mantenimiento industrial es crucial para optimizar la disponibilidad de los activos. Al identificar las causas fundamentales de las fallas, las empresas pueden implementar soluciones visuales efectivas y duraderas, evitando interrupciones en la producción y reduciendo los gastos en reparaciones innecesarias.
Otro beneficio importante del análisis de causa raíz en el mantenimiento industrial es su aplicación en el mantenimiento predictivo. Al identificar y abordar las causas fundamentales de las fallas, las empresas pueden anticiparse a los problemas antes de que ocurran, evitando paradas no planificadas y maximizando la vida útil de los equipos.
Proceso del análisis de causa raíz en el mantenimiento
El proceso del análisis de causa raíz en el mantenimiento sigue una estructura definida que ayuda a identificar y abordar de manera efectiva las causas fundamentales de las fallas en los equipos y sistemas industriales. A continuación, se describen las etapas clave de este proceso:
- Identificación del problema de mantenimiento: En esta etapa es fundamental definir claramente el problema o incidente que se desea analizar. Esto implica recopilar información relevante, como descripciones de las fallas, tiempos de ocurrencia y posibles impactos en la operatividad.
- Recopilación y análisis de datos de mantenimiento: Una vez identificado el problema, se recopilan y analizan datos relacionados con el mantenimiento de los equipos y sistemas involucrados. Esto puede incluir registros de mantenimiento, reportes de inspecciones, historiales de fallas anteriores, entre otros.
- Identificación de causas raíz de las fallas: En esta etapa se busca determinar las causas fundamentales que originan el problema. Se utilizan técnicas como el diagrama de causa y efecto, el análisis de Pareto y el árbol de fallas para identificar las posibles causas raíz. Es importante realizar un análisis exhaustivo y considerar diferentes variables que puedan estar relacionadas con las fallas.
- Selección de soluciones de mantenimiento: Una vez identificadas las causas raíz, se deben definir las acciones correctivas necesarias para solucionar el problema. Esto puede implicar implementar cambios en los procedimientos de mantenimiento, mejorar la capacitación del personal, reemplazar componentes defectuosos, entre otras medidas.
- Implementación de soluciones: En esta etapa se ejecutan las acciones correctivas definidas, asegurando que se implementen de manera adecuada y oportuna. Es importante realizar un seguimiento para verificar la efectividad de las soluciones y realizar ajustes si es necesario.
El proceso del análisis de causa raíz en el mantenimiento es iterativo, lo que significa que se puede repetir en caso de que las soluciones implementadas no resuelvan completamente el problema. Es fundamental aprender de las lecciones aprendidas y mejorar continuamente los procesos de mantenimiento para evitar futuras recurrencias de las fallas.
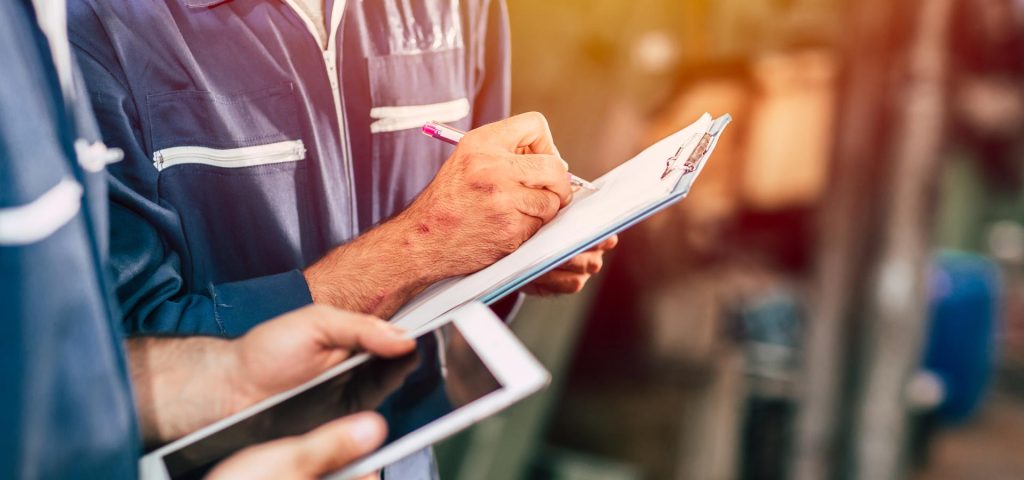
Herramientas y técnicas para identificar las causas fundamentales de las fallas
En el análisis de causa raíz en el mantenimiento industrial, existen diversas herramientas y técnicas que son utilizadas para identificar las causas fundamentales de las fallas en los equipos y sistemas. Estas herramientas permiten a los equipos de mantenimiento obtener una visión más clara y precisa de los problemas, facilitando así la toma de decisiones y la implementación de soluciones efectivas.
- Análisis de Pareto: Esta herramienta es ampliamente utilizada para identificar y clasificar las causas más frecuentes o críticas que contribuyen a las fallas. El análisis de Pareto se basa en el principio de que un pequeño porcentaje de las causas es responsable de la mayoría de los problemas. A través de gráficos y tablas, se pueden identificar las causas más relevantes y priorizar las acciones de mejora.
- Árbol de fallas: El árbol de fallas es una técnica que permite descomponer un problema o evento no deseado en causas y subcausas, estableciendo relaciones lógicas entre ellas. Esta herramienta proporciona una representación visual de las posibles secuencias de eventos que pueden llevar a una falla, lo que facilita la identificación de las causas fundamentales.
- Diagrama de causa y efecto: También conocido como diagrama de Ishikawa o de espina de pescado, esta herramienta es útil para identificar y visualizar las causas potenciales de un problema por medio de categorías o factores. Estas categorías suelen incluir métodos, maquinaria, materiales, personal, entorno y medición. El diagrama de causa y efecto permite organizar y analizar de manera sistemática las posibles causas y su relación con el problema identificado.
Otras herramientas y técnicas que se pueden utilizar en el análisis de causa raíz incluyen:
- Análisis de datos históricos y registros de mantenimiento para identificar patrones y tendencias que puedan indicar las causas raíz de las fallas.
- Entrevistas con el personal de mantenimiento y operación para recopilar información adicional sobre las posibles causas de las fallas.
- Inspecciones visuales y pruebas para identificar anomalías, defectos o condiciones inadecuadas que puedan estar causando problemas o fallas.
Estas herramientas y técnicas son utilizadas en conjunto para obtener una comprensión más profunda de las causas fundamentales de las fallas en los equipos y sistemas industriales. El análisis de causa raíz no solo permite abordar los problemas de manera efectiva, sino que también contribuye a mejorar la confiabilidad operacional y prolongar la vida útil de los activos.
Aplicación del análisis de causa raíz en el mantenimiento predictivo
En el mantenimiento predictivo, el análisis de causa raíz se convierte en una herramienta fundamental para evitar paradas no planificadas y maximizar la vida útil de los equipos. En lugar de simplemente abordar los efectos superficiales de una falla, esta metodología busca identificar las causas fundamentales que originan el problema y tomar medidas para prevenirlo.
El proceso de aplicación del análisis de causa raíz en el mantenimiento predictivo sigue una estructura similar al proceso general del análisis, pero con un enfoque específico en la identificación de las causas relacionadas con el mantenimiento. A continuación, se detallan las etapas clave en este proceso:
- Identificación del problema de mantenimiento: En esta etapa, se identifican los problemas de mantenimiento que podrían afectar la confiabilidad de los equipos. Esto implica detectar posibles fallas o eventos inesperados que puedan ocurrir en el futuro.
- Recopilación y análisis de datos de mantenimiento: Una vez identificados los problemas de mantenimiento, se recopilan y analizan los datos relevantes asociados con estos problemas. Esto puede incluir registros de mantenimiento, datos de sensores, informes de rendimiento, entre otros.
- Identificación de causas raíz de las fallas: Utilizando las herramientas y técnicas adecuadas, se busca identificar las causas fundamentales que están provocando las fallas en los equipos. Esto implica seguir un enfoque estructurado y examinar a fondo los factores que podrían contribuir a la aparición de los problemas.
- Selección de soluciones de mantenimiento: Una vez identificadas las causas raíz, se deben seleccionar las mejores soluciones de mantenimiento para abordarlas. Esto puede implicar implementar mejoras en los procedimientos de mantenimiento, cambiar componentes defectuosos, ajustar parámetros de operación, entre otras acciones correctivas.
- Implementación de las soluciones: La última etapa consiste en aplicar las soluciones de mantenimiento seleccionadas y evaluar su efectividad. Es importante realizar un seguimiento y monitoreo continuo para verificar si las soluciones están resolviendo definitivamente el problema o si es necesario realizar ajustes adicionales.
Beneficios y desafíos del análisis de causa raíz en el mantenimiento
El análisis de causa raíz en el mantenimiento ofrece una serie de beneficios significativos que contribuyen a mejorar la confiabilidad operacional de los equipos y sistemas industriales. A continuación, se enumeran algunos de los beneficios clave:
- Identificación de las causas fundamentales: El análisis de causa raíz permite determinar las causas raíz de las fallas, en lugar de abordar únicamente los síntomas o efectos superficiales. Esto permite implementar soluciones más efectivas y duraderas.
- Prevención de recaídas: Al identificar y solucionar las causas fundamentales de las fallas, se evitan recaídas en el futuro. Esto reduce los tiempos de inactividad no planificados y los costos asociados a reparaciones innecesarias.
- Mejora de la confiabilidad y disponibilidad de los activos: Mediante el análisis de causa raíz, se pueden implementar acciones correctivas y preventivas que optimizan la confiabilidad operacional de los equipos. Esto aumenta su disponibilidad y reduce las interrupciones en la producción.
- Reducción de costos: El análisis de causa raíz ayuda a identificar y eliminar las causas raíz de las fallas, lo cual se traduce en una reducción de los gastos en reparaciones y mantenimiento. Además, al evitar tiempos de inactividad no planificados, se minimizan las pérdidas económicas asociadas.
A pesar de los beneficios mencionados, el análisis de causa raíz en el mantenimiento también presenta desafíos que deben ser enfrentados para lograr resultados exitosos. Algunos de estos desafíos son:
- Complejidad de los sistemas: Los equipos y sistemas industriales suelen ser complejos, lo que dificulta la identificación de las causas raíz de las fallas. Requiere un enfoque sistemático y la utilización de herramientas y técnicas específicas.
- Disponibilidad de datos: Para realizar un análisis de causa raíz efectivo, es necesario contar con datos precisos y completos sobre las fallas y el mantenimiento. Sin una recopilación adecuada de datos, se dificulta la identificación de las causas fundamentales.
- Capacitación del personal: El análisis de causa raíz requiere de personal capacitado y experimentado en esta metodología. Es esencial contar con conocimientos y habilidades específicas para llevar a cabo un análisis riguroso.
- Intervalo de tiempo: El proceso de análisis de causa raíz puede llevar tiempo, especialmente en casos de fallas complejas. Es importante dedicar el tiempo necesario para obtener resultados precisos y evitar soluciones superficiales.
Ejemplos prácticos de identificación de causas raíz en el mantenimiento industrial
En el mantenimiento industrial, la identificación de las causas raíz de las fallas es crucial para evitar futuros problemas y mejorar la confiabilidad de los equipos. A continuación, se presentan algunos ejemplos prácticos de cómo se puede llevar a cabo este análisis de causa raíz en diferentes situaciones:
- Ejemplo de falla en un motor eléctrico:
- En este escenario, se detecta que un motor eléctrico ha dejado de funcionar. El equipo de mantenimiento realiza un análisis exhaustivo y descubre que la causa raíz del problema es el desgaste excesivo de los rodamientos del motor. Esto puede haber sido causado por una lubricación insuficiente o por trabajos de mantenimiento incorrectos. Para solucionar el problema, se implementa una rutina de lubricación adecuada y se capacita al personal de mantenimiento en las mejores prácticas para el cuidado de los rodamientos.
- Ejemplo de falla en un sistema neumático:
- En este caso, se observa que un sistema neumático ha experimentado pérdidas de aire constantes. Después de una investigación minuciosa, se identifica que la causa raíz de las pérdidas de aire son las conexiones mal ajustadas en las tuberías neumáticas. Para solventar esta situación, se lleva a cabo un proceso de reajuste y sellado adecuado de las conexiones, asegurando una adecuada estanqueidad del sistema y evitando futuras pérdidas de aire.
- Ejemplo de falla en un sistema de enfriamiento:
- En este ejemplo, se detecta un sobrecalentamiento constante en un sistema de enfriamiento de una máquina. Tras realizar una revisión detallada, se descubre que la causa raíz del problema es la obstrucción de los conductos de refrigeración debido a la acumulación de suciedad y sedimentos. Para solucionar este inconveniente, se aplica un plan de limpieza y mantenimiento regular de los conductos, evitando futuros problemas de sobrecalentamiento y manteniendo la eficiencia del sistema.
Estos ejemplos demuestran cómo el análisis causa raíz en el mantenimiento industrial permite identificar de manera precisa las causas fundamentales de las fallas, lo que a su vez facilita la implementación de soluciones efectivas y duraderas. La aplicación de este enfoque ayuda a evitar recurrencias de problemas, mejora la confiabilidad de los equipos y contribuye a maximizar la eficiencia operativa en el ámbito industrial.
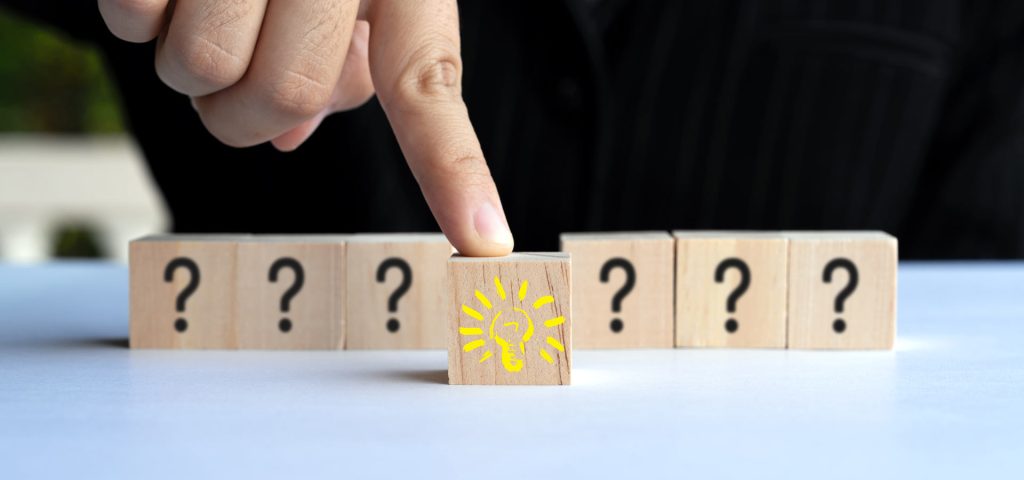